Introduction to FITOK Special Cleaning and Packaging Process Specifications

Overview of Oxygen-Enriched Atmosphere Processes
An oxygen-enriched atmosphere is usually defined as an atmosphere in which concentration of oxygen exceeds 23.5% by volume in industrial applications. Lubricants used on valves and fittings in such atmospheres must meet strict requirements. This is because non-flammable as it is, oxygen is an effective accelerant. Some materials that are non-flammable in the air can burn rapidly in oxygen-enriched atmospheres. For products used in oxygen-enriched atmospheres, FITOK offers the Special Cleaning and Packaging Process Specification (FC-02) and Grease-Free Special Cleaning and Packaging Process Specification (FOG).
1. The FC-02 process is formulated under the requirements of ASTM G93 Level C to control non-volatile residues (including grease and particles) within 66 mg/m2, and it uses oxygen-compatible non-hydrocarbon lubricants. When products need lubricating and are used in oxygen-enriched atmospheres, it is highly recommended to choose the FC-02 process.
2. The FOG process, a process specification developed in response to customer requests, does not allow lubrication on wetted surfaces on the basis of the FC-02 process. The FOG process is suitable for media with high purity requirements.

Impact of the FOG Process on Products
The FOG process specification prohibits using any lubricant on wetted surfaces of products. The absence of lubrication leads to increased friction between components. To ensure product operability, we reasonably lower the maximum working pressures of valves. For instance, for BO series straight ball valves with an orifice of 0.19 in. (4.8 mm), the maximum working pressure declines from 3000 psig (207 bar) to 500 psig (34.4 bar). Likewise, for BO series straight ball valves with an orifice of 0.41 in. (10.3 mm), the maximum working pressure declines from 2500 psig (172 bar) to 200 psig (13.8 bar).
For BGP series ball valves, which are also suitable for oxygen-enriched atmospheres and the FOG process specification, it is possible to differentiate the BGP series from BO series by the working pressure, working temperature, orifices, etc. Under the same conditions, it is advisable to give priority to the BGP series for high purity pipelines, because the BGP series has a helium leak rate ≤ 1x10-8 std cm3/s and a standard average internal surface roughness of Ra 25 μin. (0.6 μm). Below is a comparison of some parameters of the two series after applying the FOG process.
Valve | Max. Working Pressure | Working Temperature | Average Internal Surface Roughness | Leak Testing | Orifice | Structure |
BO Series | 10.3 mm orifice: 200 psig (13.8 bar) |
-65 °F to 300 °F (-54 °C to 148 °C) |
Ra 125 μin. (3.2 μm) | Bubble testing | 0.05 in. to 0.41 in. (1.3 mm to 10.3 mm) |
2-way (Straight, Angle), 3-way, 4-way, 5-way, 6-way, 7-way |
Other orifices: 500 psig (34.4 bar) |
||||||
BGP Series | 1000 psig (69 bar) | 20 °F to 450 °F (-28 °C to 232 °C) |
Ra 25 μin. (0.6 μm) | Bubble testing, helium leak testing (optional) | 0.18 in. to 0.79 in. (4.6 mm to 20.0 mm) |
Straight |
Additionally, the FOG process also influences the selection of seat materials. The reason is that different materials have varying friction coefficients, and the FOG process prefers materials with low friction coefficients. For instance, PEEK has better mechanical strength and elastic modulus than PTFE, but its dynamic friction coefficient is one order of magnitude higher than PTFE. Therefore, it is not recommended to choose a PEEK valve seat when using the FOG process.
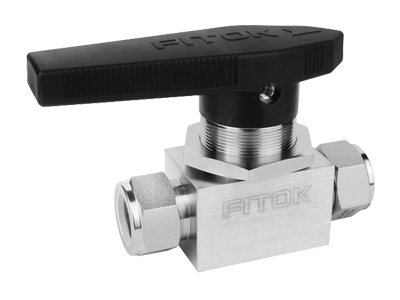
BO Series Ball Valve
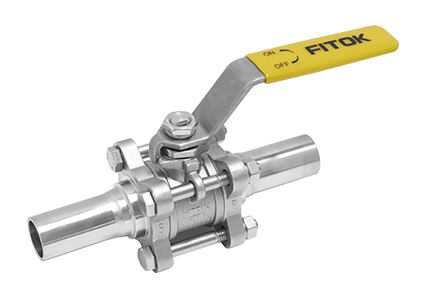
BGP Series Ball Valve

Comparison of FITOK Cleaning and Packaging Process Specifications
FITOK offers four different cleaning and packaging standards for customers to choose from, depending on their specific working conditions and requirements. Here’s a comparison of these standards:
Process Specification | Standard Cleaning and Packaging Process Specification (FC-01) | Special Cleaning and Packaging Process Specification (FC-02) | Grease-Free Special Cleaning and Packaging Process Specification (FOG) | Ultra-High Purity Process Specification (FC-03) |
Raw Material | Follow the design | Follow the design | Suitable for high purity environments | |
Lubrication | Molybdenum disulfide-based or silicone-based grease used on wetted components | Oxygen-compatible nonhydrocarbon lubricant used on wetted components | No lubricant allowed on wetted surfaces | No lubricant allowed on wetted surfaces |
Assembly Environment | Ordinary clean workshop | Cleanroom | Cleanroom | |
Testing | Bubble testing, helium leak testing | Bubble testing, helium leak testing | Helium leak testing | |
Packaging | Single packaging | Double packaging | Double packaging | |
Application | Oil & Gas, Power & General Equipment Manufacturing, etc. | Bulk Gases, Photovoltaics, etc. | Ultra-pure Water, Pharmaceutical Industry, etc. | Integrated Circuits, etc. |
Related Articles: